KEMUTEC SIEVE / CONE MILL COMBINATION MACHINE
or
Call 216-409-1394
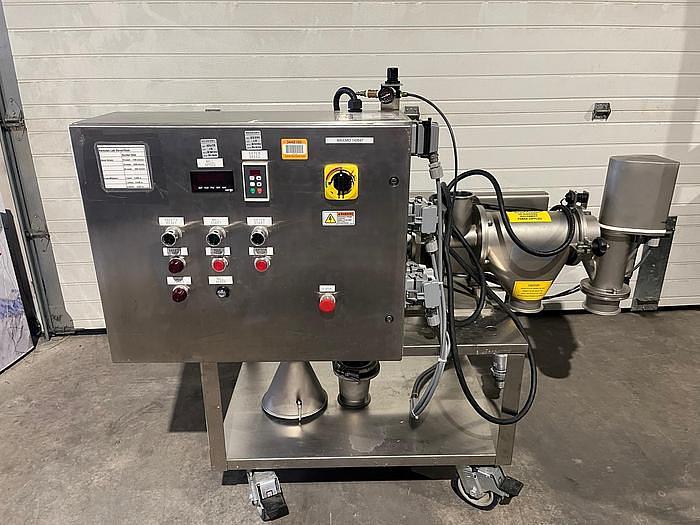
Description
1 - USED KEMUTEC SIEVE / CONE MILL COMBINATION MACHINE
- Designed to Both Sieve/Sift & Mill Product to the Desired Particle Size
- The Cone Mill is Fitted to the Sifter Oversize Outlet
- Oversize Product That Passes Through the Sifter is Then Milled in the Cone Mill
- The Sifter Fines Outlet and the Cone Mill Outlet Both Feed into a Single Common Outlet Hopper
- Comes with Integrated Control Panel for Sifter and Mill Speed, Start/Stop and Emergency Stop
- 3/60/230 Volts. Requires Air
- Sifter Operation: Material is Fed Via the Sifter Inlet Chute into the Feed Auger Screw. The Feed Auger Conveys the Material into the Cylindrical Sifting Chamber at a Controlled Rate Where it is Picked up by a Rotating Paddle Assembly and Thrown Centrifugally Against the Sieve Basket Mesh. The Blades on the Paddle Assembly are set in a Slight Forward Helix Configuration to Traverse the Material Along the Whole Length of the Basket Mesh. The "Fines", or (Below Sieve Size Product), Passes Through the Screen and is Collected at the Fines Outlet. The "Overs" Material is Then Conveyed to the Cone Mill for Further Processing.
- Cone Mill Operation: The Cone Mill is Designed for a Wide Range of Applications. Applications Upon Which the Cone Mill Will be Most Effective Can be Characterized as Follows:
- 1. Products Requiring Mechanical Size Reduction with Minimum Inter-particle Comminution.
- 2. Relatively High Size Reduction Ratios with Associated Large Feedstock Sizes.
- 3. Softer or Fatty Products Which Would Blind or Clog More Conventional Systems.
- The Mill Relies Upon the Action of a Beater Rotating Inside a Perforated Cone at Between 1,000 to 5,000 RPM. Product Falling Into the Mill is Rapidly Given Rotational Energy Both From Impact With the Beater and the Swirling Air Regime Present in the Cone. The Effect of This Rotational Energy is to Throw the Product Out Onto the Cone Wall Where Size Reduction Rakes Place Under a Combination of Mechanical Impact and Shear Forces Generated by Friction Between the Moving Product and Stationary Cone Wall. Immediately After Size Reduction the Ground Material is Expelled Through the Cone Perforations by Centrifugal Force, Thus Preventing Re-agglomeration. A Further Advantage of the System is That the Perforated Cone Forms a Good Heat Sink and Minimizes the Degradation of Heat Sensitive Products.
Specifications
Manufacturer | Kemutec |
Model | Lab/CM075 |
Year | 2008 |
Condition | Used |
Stock Number | 11005 |